Thanks Paul
I can let you know how I did that if it can help (but remember I'm not a pro)
As I'm at work I cant show you a picture of me holding the dremel at work, I developped for this time (never too late to progress

) a new way to handle it, pictures tomorrow
I think it's important to have a good drawing of the inlay... I use a CAD software (for the New yorker), or a .jpg file of the inlay printed at right scale (double check+++)
Then you glue the paper on the wood using spray neoprene glue. This glue doesnt wet the paper as white glue does, and paper is easy to remove when the job is done
Then carefully cut the paper and the wood fibers a little OUTSIDE the drawing with an XACTO (I did it too near from drawing and it was painfull to enlarge the cavities with a scraper I grinded in a razor blade:
I use magnifying lenses to do that
Then rout with the dremel. If your XACTO job was good, you'll get clean cavities without pieces of paper coming inside the cavities.
Hold the dremel router base with TWO hands, facing you, and use a piece of wood as armrest (you can see it below). My previous inlay works were not done this way and this one is really better
AND, I built a foot switch for the Dremel, really helps too
Then enlarge the cavities as necessary, the best tools are sterwmac micro chisels and a small home-made scraper...
I'll be away from home for work the next 2 weeks, no lap steel building...
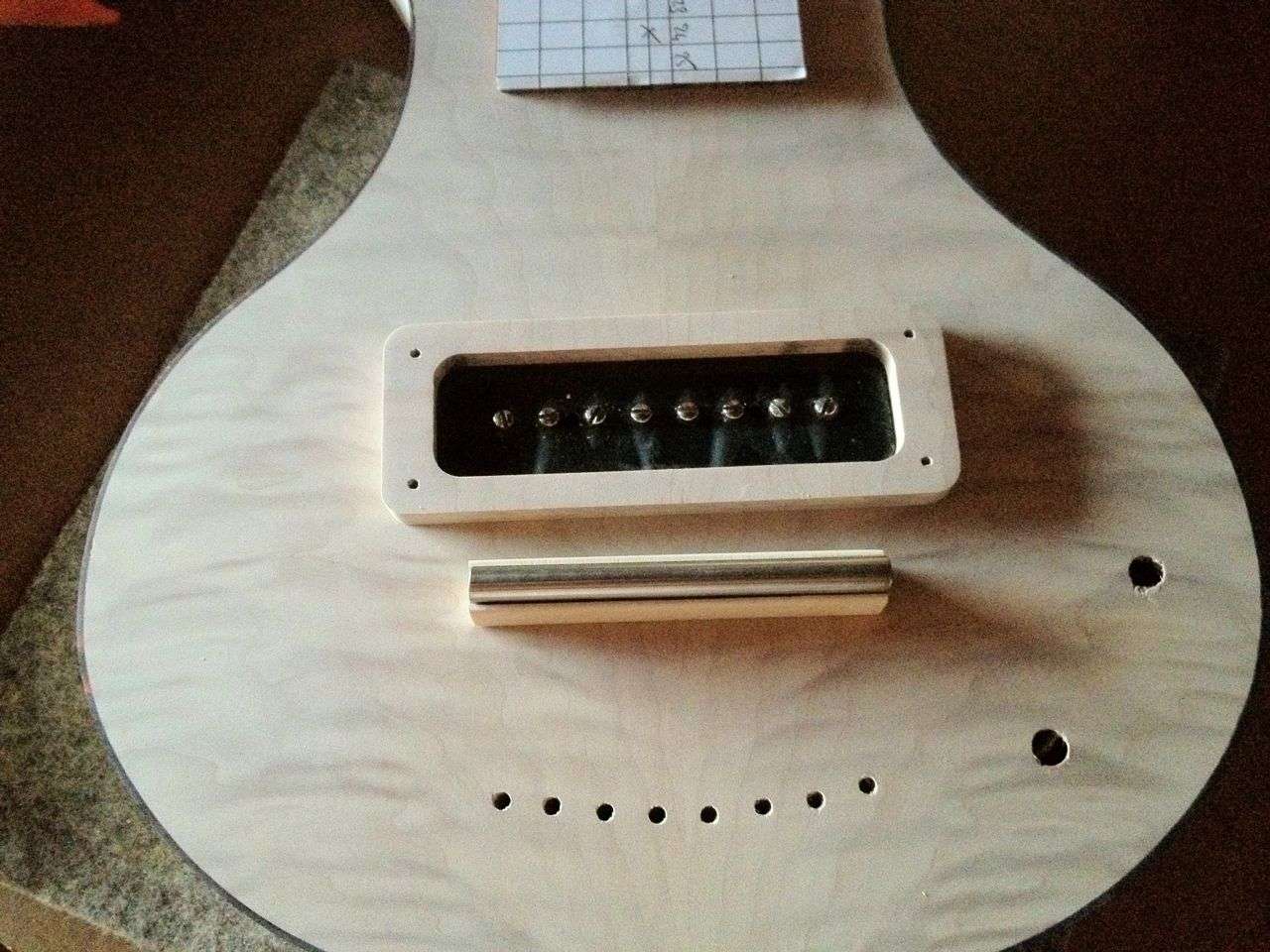